In industrial and manufacturing settings, unplanned equipment downtime can result in massive losses, from production delays to damaged machinery. This is where the power of energy monitoring and preventative maintenance comes into play, particularly with advanced software features like “triggers.”
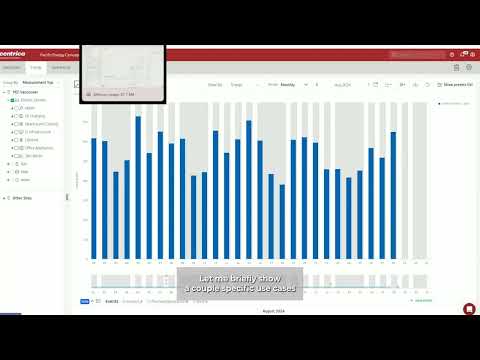
The Role of Triggers in Energy Monitoring
Alert Triggers are a critical feature when using energy monitoring systems for preventative maintenance and machine health monitoring.
With a “triggers” function, maintenance and operational teams can customize alerts based on specific machine thresholds or behaviors. For example, if a machine starts operating outside its normal parameters — such as a spike in current draw, off-schedule operation, or increasing startup times — alerts can immediately notify operational teams via email or phone. This proactive approach enables quick action without requiring constant monitoring.
Real-World Application: Avoiding Costly Shutdowns
Recently, one of our Energy Monitoring customers — a global supplier of rubber products for the Defense & Aerospace industry — was able to leverage custom triggers to detect a deviation in the phases of a compressor in one of their manufacturing plants. The 3-phase power draw of this particular machine, which typically showed a 10–15% deviance between phases when operating correctly, had begun to show an escalated current draw with one of its phases. This can be a leading indicator of a motor shorting. This condition, if unnoticed, could have led to motor failure, tripped breakers, and shutdowns, potentially costing the facility hundreds of thousands of dollars in lost production.
Using energy monitoring data, the team identified the issue early and was able to investigate the issue before a failure event. This preventative maintenance approach avoided unplanned downtime and associated costs, showcasing the immense value of having real-time operational insights.
The Preventative Maintenance Advantage
Preventative maintenance, supported by features like energy monitoring alerts, allows facilities to:
- Detect and address anomalies before they escalate.
- Schedule repairs or replacements during planned downtime.
- Minimize operational disruptions and avoid financial losses.
- Extend equipment life by addressing issues early.
By integrating energy monitoring solutions with alert-based systems, facilities can shift from reactive to proactive maintenance strategies, ensuring smoother operations and cost savings.
Getting Started with Energy Monitoring: What to Expect
Working with our team at Pacific Energy Concepts (PEC), you access an expert partner to deploy an intelligent energy monitoring system that works for your business — without needing to sideline other projects or get pulled away from your daily workload.
Our 3-step process is simple:
- Step 1: Schedule an Intro Call with a PEC Sales Engineer: Get to know our team and discuss your project with an Energy Monitoring expert.
- Step 2: PEC Begins Scoping Your Project: We’ll begin working with key stakeholders to develop a system that’s designed for your needs and goals.
- Step 3: Approve & Implement: We’ll walk you through the different proposal options, discuss the pros and cons, and work with you to determine the best path forward.
Once you press go, PEC Project Managers will join the process to begin overseeing your project implementation — acting as your dedicated project leader to manage everything from installation to training your team on the software.
Get started today! Fill out the form at the link below and we will follow up to schedule your intro call.