Retail prices for electricity continue to see unprecedented growth throughout the US. According to the EIA’s 2022 Census, the average cent per kilowatthour across all sectors saw an increase of over 17% from September 2021 to September 2022 — rising from 11.59 to 13.52.
Furthermore, the industrial sector continues to be one of the most affected segments, facing an average cent/kWh Hour increase of over 23%, including some states that saw increases of over 30% (New York in particular faced an increase of 125% in the industrial sector).
While a portion of these increases can be attributed to economic rebounds from the covid pandemic, along with Russia’s ongoing war in Ukraine that jumpstarted an energy crisis throughout Europe, another significant factor of rising energy costs is the increasingly hot and humid summers across the US, which has led to an increasing demand for power.
With little optimism for decreasing energy costs in the near future (the EIA has forecasted average retail prices will continue to climb in 2023 in their recently published Short-Term Energy Outlook report) business leaders and facility management teams are seeking ways to get a handle on this rising energy spend.
Technologies to reduce energy spend in industrial facilities
The good news is, building efficiency is a thriving and rapidly evolving space, with new and established technologies on the market that can lead to dramatic reductions in annual energy usage. Learn how you could potentially uncover massive reductions in your energy spend with these 4 key technologies below.
1. Commercial Energy Monitoring System
Historically, businesses have depended on energy use data provided by their power providers to understand how much electricity is being consumed at their facilities. These utility reports will typically provide measurements of top-level electricity use throughout each day, broken out in intervals as granular as of every 15 minutes, which energy management teams can then use to manually calculate (or make reasonable estimates) about how energy consumption then travels throughout the facility.
While this data continues to be vital for measuring and verifying overall energy use, it is limited in helping organizations understand exactly which components of their facility are demanding the most power.
Commercial energy monitoring systems allow business leaders to fill that data gap. Innovations in IIoT have led to the development of monitoring sensors (known as current transducers, or “CT’s”) that can be installed throughout a facility to more effectively measure the energy demands of each device consuming power. This includes machines, compressors, motors, lighting, HVAC systems, and more, helping businesses pinpoint exactly how energy travels in their facility after the meter.
This device-level data offers several key advantages for energy management teams:
- Quickly and accurately gather energy use data for measurement and verification;
- Confidently determine the biggest opportunities for efficiency gains, and;
- Receive real-time alerts for failing machines, as well as quickly identify devices seeing erratic power consumption that may signal potential issues or the machine nearing end of life.
These systems are typically comprised of a hardware+software solution that includes 3 key components:
- Monitoring and Metering Sensors: Monitoring sensors are small current transducers that easily snap-on to the wires running power to each device in the facility (typically installed in a sub-panel). Theses sensors take real-time measurements of the electrical flow running through to the machines, capturing the amount of power each device is consuming. Metering sensors are installed higher up in the electric hierarchy (i.g. a main electrical panel) and combine the overall electrical current with the facility voltage to measure the overall power quality of the facility. These 2 components help create a comprehensive picture in real time of a facility’s energy use.
- Data Bridge: As sensors take a measurement, they will transmit the data over to a data bridge, which will then securely transmit the data to an online monitoring dashboard where the measurements can be viewed.
- Close-based Monitoring Dashboard: The monitoring dashboard is where admins can login online to view all of the real-time and historical measurement data. Some portal features will naturally vary depending on the monitoring solution, but most will include features that allow users to visualize measurement data use throughout the facility, drill down to energy use by device (or device category), see historical trends, and customize notifications for users within the system.
Energy monitoring systems can be a transformational tool for commercial and industrial spaces, and any management team that’s interested in maximizing efficiency could strongly benefit from first measuring exactly how energy is used, then leveraging that data for more informed decision making.
2. LED Lighting Retrofit
Transitioning from older lighting technologies, like fluorescent or incandescent bulbs, to an LED system is one of the most effective ways that industrial facilities can reduce their energy waste. In particular, large facilities that operate 24/7 or have long operating hours (e.g. warehouses, manufacturing plants, distribution centers, industrial facilities, etc.), will typically see the most impact, unlocking savings in energy spend that can potentially range from hundreds of thousands to millions of dollars each year.
This is due to a couple of key advantages that LED possesses over incumbent technologies:
- Energy efficiency: LED bulbs use up to 90% less energy than incandescent bulbs, and;
- Longer life expectancy: Optimized LED fixtures can drastically increase the life expectancy of a bulb, with a lifespan of +100,000 hours.
This equates to 11 years in operation at a 24/7 operational facility before needing replacement!
In addition to the above advantages, facilities can further improve lighting efficiency by optimizing the lighting design, rather than just replacing existing bulbs with 1:1 LEDs.
Combining LED’s brighter light levels with its ability to direct light precisely where it is needed most, transitioning to an LED system may also reduce the overall number of fixtures needed in the facility (often significantly) in order to adequately light the space.
Customers that work with PEC to deploy industrial LED retrofits have seen their annual energy spend reduced by margins greater than 80%. See our work below to learn how your facility could benefit from an upgraded lighting system.
3. Advanced Lighting Control Systems
Another efficiency advantage of LED technology is the ability to incorporate fixtures into a smart lighting control network. These advanced control systems allow facilities to automatically monitor, adjust, and optimize light levels within defined zones or at the individual fixture level quickly, easily, and at all times.
Control systems are able leverage several key features to optimize light levels and significantly improve energy efficiency:
- Daylight harvesting: Fixtures are programmed to monitor and automatically adjust light levels depending on the existing natural daylight in a particular space
- Occupancy sensors: Motion sensors that monitor current occupancy in the space and adjust based on activity
- Task tuning: Light levels are optimized based on how the space is being used, allowing for less energy output for certain tasks that may require less light
- Zone management: Control multiple areas or zones in the facility based on parameters you’ve set
- Scheduling: Timers set to automate lighting based on time of day
- Reporting: Real time data that provides detailed information about the current performance and health of your lighting system
One PEC client that found huge success with advanced control systems was Alaska Airlines, who leveraged daylight harvesting in their airport hangars to auto-adjust the fixture light levels as the natural light changed throughout the day — helping them in their efforts of reaching net-zero carbon emissions by 2040. Here the team at Alaska Airlines discuss the motivations behind this project below:
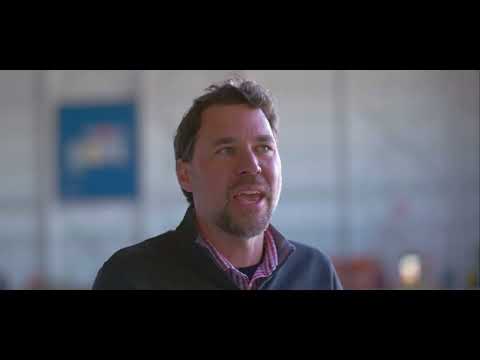
4. HVAC Smart Motor Retrofit
A rapidly evolving technology with huge potential to reduce industrial energy consumption is smart motors in HVAC systems. Currently, fixed-speed motors in Roof-top Units (or RTU’s) are typically used to power commercial HVAC systems, which inefficiently consume large amounts of power when heating or cooling a space. Because of their “fixed speed” design, these systems do not have the capability to adjust facilities to cooler or warmer temperatures using an optimal motor speed, which leads to excessive amounts of energy being wasted in the process.
As a result, electric motors are currently responsible for over 45% of the world’s electricity usage.
Smart motors have simplified HVAC systems to run more efficiently. Using “cycling” technology, motor speeds in these systems are able to ramp up to meet calls for heating & cooling, then cycle back down to a more energy efficient ventilation mode after the temperature has been adjusted. This cycling capability has the potential to provide an energy savings of 45-55% for businesses that retrofit the existing fixed-speed motors in their RTU’s.
Furthermore, these smart motors also come with an improved software technology that provides real-time data around the HVAC system. This data visibility can be extremely valuable for facility management and maintenance teams to track when there are signs of degradation or faults with the system, granting them the ability to take quick action to alleviate issues before failures occur.
More info on HVAC Smart Motors here:

Learn how PEC can help you take control of your energy use
Taking the time to identify your efficiency goals, learn your biggest opportunities for improvement, and understanding your potential ROI are all important first steps toward gaining control of your energy output.
Our team at PEC is here to help you get started with the process. Get in touch using the form below to connect with one of our experts and learn how we can potentially make an impact at your facility.